Robot Overview
Laelaps II is a 40 Kg quadruped robot with 3-segmented legs built by the Legged Team at the NTUA-CSL. The robot was optimally designed using a combination of criteria related to forward speed, energy efficiency and stability, based on both analytical and optimization-based studies. The mechanical and electrical subsystems were designed and manufactured in-house using SOTA methods and materials such as carbon fiber and duralumin. High-end embedded computers are used in an EtherCAT network enabling real-time high bandwidth data exchange between all subsystems. Special hardware accelerators are used to achieve high control frequencies. All SW has been designed optimally resulting in an efficient mixture of ROS-enabled computers running Real-Time Operating System (RTOS) and bare metal approaches. High-end reliable electric motors are used together with lightweight high power motor drives. A well-instrumented experimental environment is available which includes a varying inclination and speed treadmill, cameras, power supplies etc.
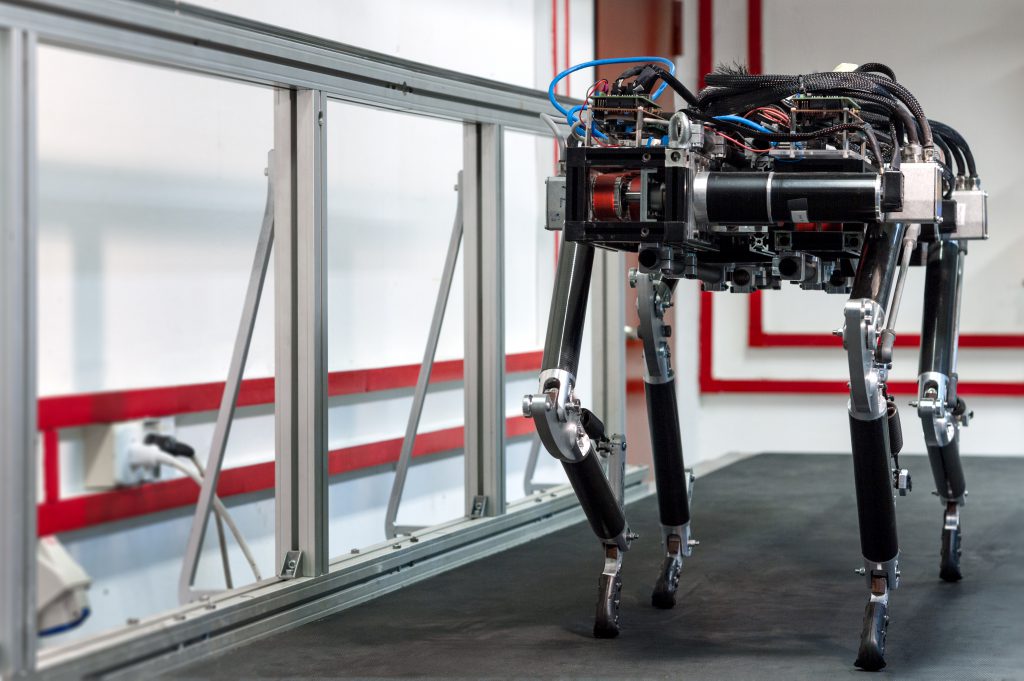
Leg Design
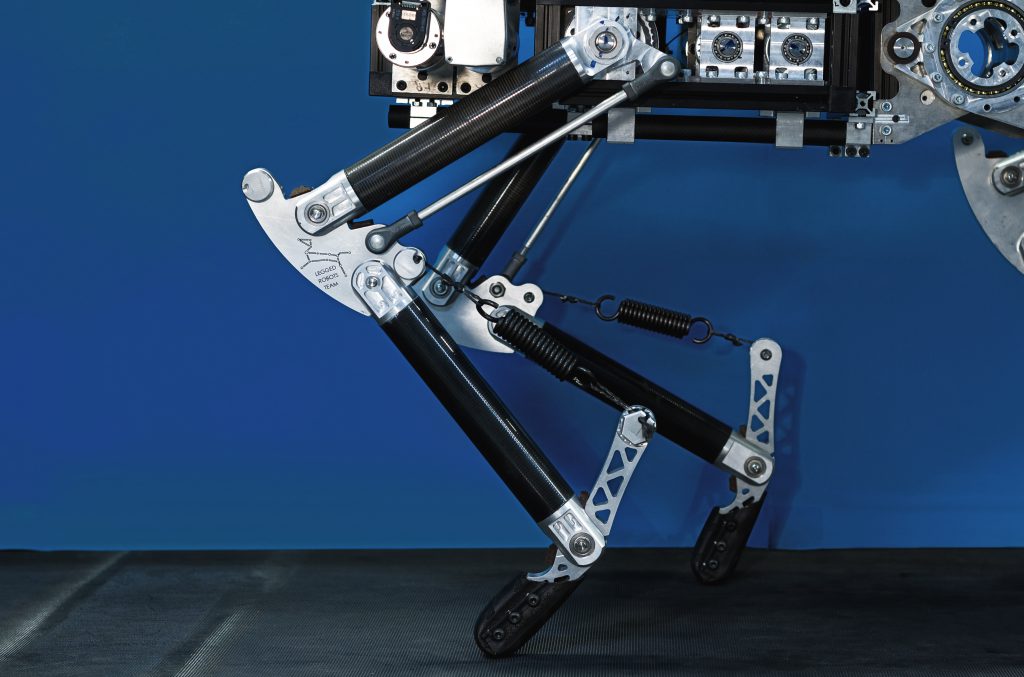
Each leg is comprised of three segments, the lengths of which were the result of both analytical and optimization-based studies of the NTUA-CSL’s research team, searching for optimal – in terms of energy efficiency, speed, and stability – combinations of segment lengths, robot properties (e.g. actuation limitations, robot mass etc.) and gait characteristics (e.g. type of gait, stride length/ frequency etc.). The actuation system of each leg, comprises of two electric motors combined with gearboxes and belt-pulley transmission systems. Since the knee motor is mounted on the body, a parallel mechanism is used to drive the distal leg segments. The two distal segments are connected via a tendon-like spring. A wide variety of springs are available to adjust to different environments and applications.